Our General Specification for PCB Board Production
Purpose: To clarify PCB production requirements, reduce PCB production problems, facilitate communication with PCB manufacturers, and unify the standards of various departments of the company and PCB manufacturers.
Scope of application: company PCB prototyping and production board content.
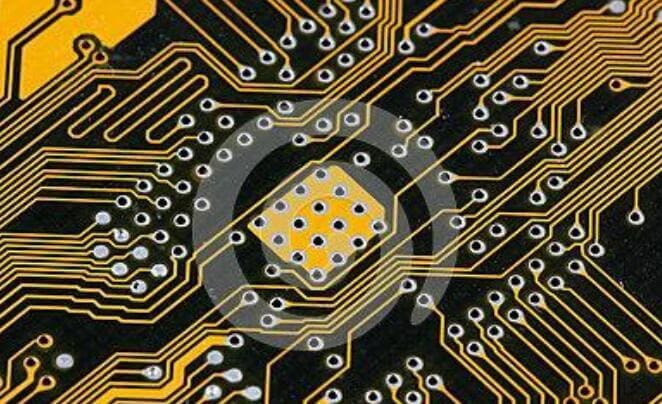
- The PCB board, quantity, process requirements, etc. are made according to the requirements of the PCB contact form (the production board is subject to the signed sample).
- The way of boarding and the size of the structure are subject to the PCB file and the boarding drawing. If there is a deviation between the two, please contact our PCB engineer for confirmation.
- The PCB production contact form needs to be sent out together with the PCB information. The PCB manufacturer should reply by email immediately when receiving the PCB information from our company. The information has been received.
- For PCBs that have not been signed and made first, we need a written document from our company (it can be an E-mail document or fax).
- When PCB samples are made together, the samples and the goods should be packaged separately, and the quantity should be sent as required.
- All PCB samples should be marked with the board number, the receiving department and the name of the consignee (tentatively designated by each purchasing department) on the packaging.
- When the sample cannot be returned on time, the designated personnel of our purchasing department and the development engineer shall be notified in time to explain the reason and the delivery date.
- Each PCB board must be printed with the manufacturer’s logo and production date (cannot be written in Chinese, cannot be covered by components, and cannot be printed with other content. Please confirm with our PCB engineer when the PCB is too small to be printed).
- Our PCB board generally uses green oil for solder mask, silk screen oil for double-sided, multi-layer, and carbon oil boards all use white silk screen oil, single-panel component surface uses white silk screen oil, and welding surface uses black silk screen oil.
- The silk screen should be clear, the green oil should be high temperature resistant and not easy to fall off, the entire PCB board should not have dirt or scratches, and the pads should be easy to tin.
- The maximum deformation of a single-sided PCB must be less than 1% of the diagonal of the PCB, and the maximum cannot exceed 2.0mm. The maximum deformation of a double-sided multi-layer PCB must be less than 0.8% of the diagonal of the PCB, and the maximum cannot More than 1.0mm.
- PCB thickness tolerance of PCB thickness ≥1.2mm must be ≤±0.14mm, PCB thickness tolerance of >0.8mm≤1.0mm must be ≤±0.10mm, and PCB thickness tolerance of <0.8mm must be ≤±0.06mm.
- The tolerance of all die punching round holes must be ≤±0.1mm, the tolerance of the second drill for computer drilling must be ≤±0.05mm, and the tolerance of all non-round holes must be ≤±0.15mm.
- All the rounded corners and rectangular holes of the PCB shape should be in place (the boards with manual gong holes that are not mold-opened shall not affect the production of our company).
- The external dimension tolerance of PCB must be ≤±0.1mm. The external dimension tolerance of PCB with side length greater than 200mm must be ≤±0.15mm. PCB shape tolerances with side lengths greater than 400mm need to be ≤±0. 2mm
- All vias ≤0.5mm should be plugged with green oil (green oil should be painted on both sides, and the IC position should be 100% green oil plug holes. Tin beads and green oil plug holes are not allowed in the through holes. The emergence of the board surface must be ≤±0.15mm), the total number of other unplugged holes cannot be more than 10 people per board, and the vias above 0.5mm should be plugged as far as possible.
- Green oil bridges should be made between the pads with a distance greater than 0.4mm between the pads of the components, and the pads with a distance less than 0.4mm do not need to be made. Our company has designed a solder mask silkscreen oil to be used on the welding surface of the socket and other positions. When the distance between the discs is greater than 0.3mm, the bridge should be clear. This silkscreen oil can be slightly applied to the edge of the pad but needs to be ≤0.1mm.
- Double-sided board, multi-layer board plug-in components do not open the green window on the plug-in surface, and the copper can be exposed ≤0.15mm, and the copper plating in the socket needs to be tinned.
- The line width error of copper foil should be less than ±20 design line width.
- The stamp hole is made according to the mechanical drawing. The V-CUT requirements are as follows: All single-sided 94V0, 94HB materials are retained after 0.4±0.2mm after V-CUT, other materials are retained in the middle of VCUT 0.4±0.2mm, double-sided and multi-layer boards are at 1.0 Leave 0.4±0.1mm in the middle of the PCB V-CUT above mm, 0.3±0.1mm in the middle of the PCB V-CUT with a thickness of 0.6mm-0.8mm, and leave 0.2-0.3mm on one side of the PCB with a thickness of less than 0.6mm. In the case of V-CUT, if the edge of the V-CUT has no gap in the middle, try to lower the tolerance and keep the small point. If the gap in the middle is longer and the edge joint is less than 2/3 of the full side, try to use the tolerance as far as possible, and keep the larger point.
- All PCB boards need to use 0.5-1.0 oz/cm² copper thickness plates.
- The deviation of the silk screen and the pad and the drilling must be ≤±0.25mm, and the deviation of the center position of the drilling must be ≤±0.05mm.
- If you find that the information is suspicious or has obvious errors during production, please contact our PCB engineer for confirmation.
- Other places with special requirements are made as required.
- The places not covered by this code shall be inspected according to IQC acceptance.