Characteristic
● Surface mount technology (SMT) is adopted;
● Extremely effective treatment of heat diffusion in circuit design scheme;
● Reduce product operating temperature, improve product power density and reliability, and prolong product service life;
● Reduce product volume and reduce hardware and assembly costs;
● Replace fragile ceramic substrate to obtain better mechanical durability. Structural aluminum based copper clad laminate is a metal circuit board material, which is composed of copper foil, thermal insulation layer and metal substrate. Its structure is divided into three layers:
Circuit layer: copper clad laminate equivalent to ordinary PCB, with circuit copper foil thickness of LOZ to 10oz.
Dielcctric layer: the insulating layer is a layer of low thermal resistance and heat conduction insulating material. Thickness: 0.003 “to 0.006” inch is the core technology of aluminum based copper clad laminate, which has obtained UL certification.
Base layer: it is a metal substrate, generally aluminum or optional copper. Aluminum based copper clad laminate and traditional epoxy glass cloth laminate.
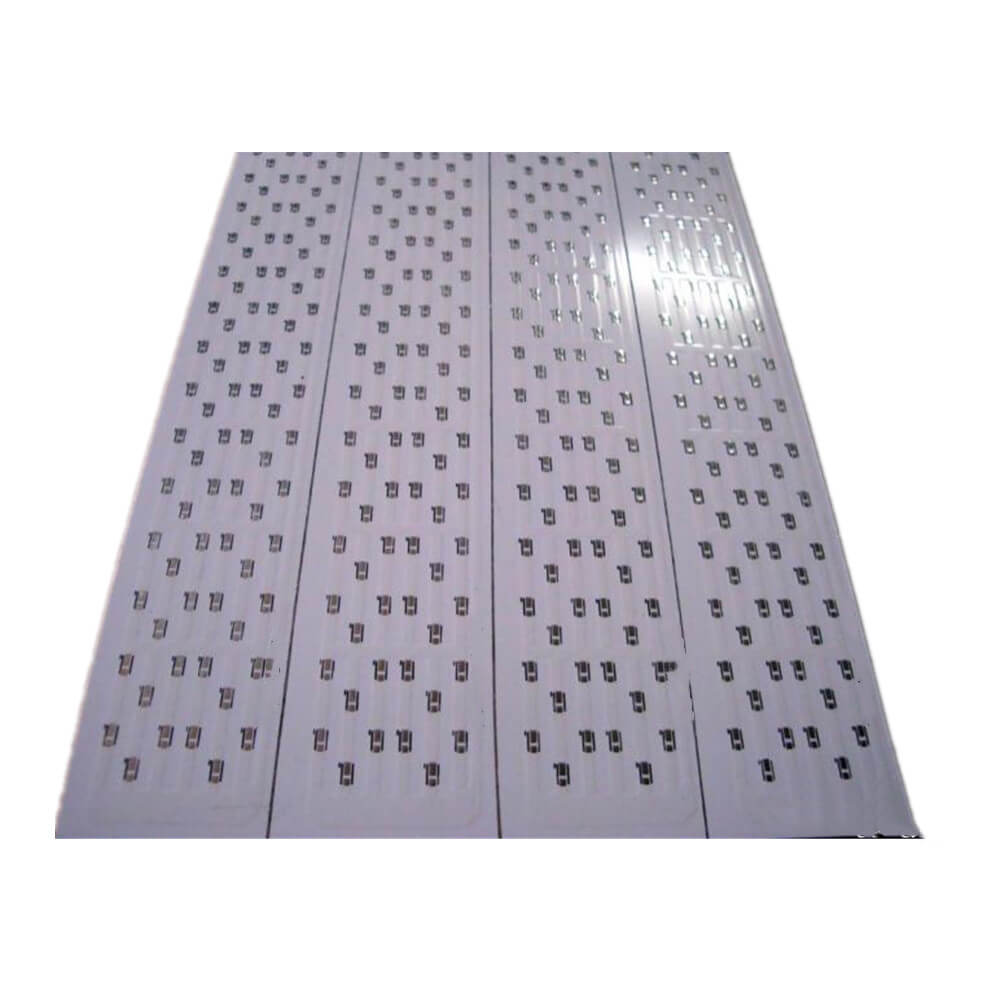
Compared with other materials, PCB has incomparable advantages. Suitable for SMT public art of surface mount power components. Without radiator, the volume is greatly reduced, the heat dissipation effect is excellent, and the insulation and mechanical properties are good.
The LED grain substrate is mainly used as the medium for heat energy export between the LED grain and the system circuit board, and is combined with the LED grain through the process of wiring, eutectic or cladding. Based on the consideration of heat dissipation, the LED grain substrates on the market are mainly ceramic substrates, which can be roughly divided into thick film ceramic substrates, low-temperature CO fired multilayer ceramics and thin-film ceramic substrates according to different line preparation methods. In traditional high-power LED components, thick film or low-temperature CO fired ceramic substrates are mostly used as grain heat dissipation substrates, Then, the LED grains are combined with the ceramic substrate by gold wire. As described in the preface, this gold wire connection limits the efficiency of heat dissipation along the electrode contact. Therefore, large factories at home and abroad are working hard to solve this problem. There are two solutions. One is to find a substrate material with high heat dissipation coefficient to replace alumina, including silicon substrate, silicon carbide substrate, anodized aluminum substrate or aluminum nitride substrate. The semiconductor characteristics of silicon and silicon carbide substrate make it encounter a more severe test at this stage, The anodized aluminum substrate is easy to be conductive due to fragmentation due to its insufficient strength of anodized oxide layer, which limits its practical application. Therefore, at this stage, aluminum nitride is more mature and generally accepted as the heat dissipation substrate; However, the aluminum nitride substrate is not suitable for the traditional thick film process (the material must be subjected to 850 ℃ atmospheric heat treatment after silver glue printing, resulting in the problem of material reliability). Therefore, the aluminum nitride substrate circuit needs to be prepared by the thin film process. The aluminum nitride substrate prepared by the thin film preparation process greatly accelerates the efficiency of heat from the LED grain to the system circuit board through the substrate material, so it greatly reduces the burden of heat from the LED grain to the system circuit board through the metal wire, so as to achieve the effect of high heat dissipation.