–The difference of gross profit rate between large and small batch board manufacturers is obvious
Printed circuit board is the key electronic interconnection component of electronic products. It’s known as the “mother of electronic products”. The downstream of printed circuit board is widely distributed, covering communication equipment, computer and its surrounding, consumer electronics, industrial control, medical, automotive electronics, military, aerospace science and technology and other fields. Irreplaceable is one of the factors for the stable development of printed circuit board manufacturing industry.
The development of printed circuit board in China started late, and the high-end technology of PCB production lags behind the developed countries.
China began to carry out the research and development of printed circuit board in 1956. Compared with developed countries, China has lagged behind nearly 20 years before it began to participate in and enter the PCB market. The concept of printed circuit first appeared in the world in 1936. It was put forward by a British doctor named Eisler, who pioneered the related technology of printed circuit copper foil etching process.
In recent years, China’s rapid economic development, coupled with policy support for high-tech, China’s printed circuit board in a good environment to develop rapidly. 2006 is a landmark year of PCB development in China. This year, China successfully surpassed Japan and became the largest PCB production base in the world.
With the advent of 5g commercial era, the major operators will invest more in 5g construction in the future. So they need to speed up the update speed of printed circuit board technology in China. However, China is only a big manufacturing country of printed circuit in the world at present, but it is not a powerful country. Many technologies still lag behind the developed countries such as the United States, Japan and Europe.
The development of China PCB Manufacture Industry
1956
China began PCB development. ·
The 1960s
The panel is produced in batch, and the double-sided plate is calibrated in small batch production and the multi-layer board is developed. ·
The 1970s
Due to the limitation of the historical conditions at that time, the development of PCB technology is slow, which makes the whole production technology lag behind the advanced level of foreign countries.
The 1980s
The advanced production lines of single, double-sided and multilayer printed boards were introduced from outside the park, which improved the production technology level of printed boards in China. ·
1990s
Hong Kong, Taiwan and Japan and other foreign PCB manufacturers have come to our Park joint venture and sole proprietorship to set up factories, making our printed board production and technology leapt forward..
2003
PCB output value and import and export value both exceeded US $6 billion, surpassing the United States for the first time, becoming the second largest PCB manufacturer in the world. The proportion of output value also increased from 8.54% in 2000 to 15.30%, nearly doubled. ·
2006-2016
China has replaced Japan and has become the most active manufacturer of PCB production and technology in the world. The PCB industry in China has maintained a high-speed growth of about 20%, which is far higher than that of the global PCB industry. Develop the technology of graphic manufacturing, laser drilling and surface coating, detection and so on.
Although in 2006, China’s PCB output value exceeded that of Japan and became the world’s largest PCB manufacturer. But few manufacturers of PCB templates with high technology content.
The production process of PCB template mainly includes new product research, test, development and pilot test. The order characteristics of this kind of PCB are small area and many categories. Therefore, the area of a single order of PCB template is generally less than 5 square meters. The positioning of PCB template enterprises is to provide customers with the above services. Compared with batch board enterprises, customers have higher requirements for the response speed of template factories. Therefore, the template factories need to provide more services To have stronger production organization and customer management ability (management and quality control) is also one of the core competitiveness of model enterprises.
Batch board refers to the PCB products that have sufficient commercial value and can start mass production after passing the stage of R & D and trial production. Therefore, batch board is used in the stage of commercialization and large-scale production of products, and the order area is usually more than 5 square meters, so it has higher requirements for large-scale production capacity of enterprises.
Both large batch and small batch boards show the characteristics of customization, but the gross profit rate of small batch board manufacturers is higher.
There are many kinds of PCB classification methods, which can be divided into template and batch board according to customer demand; according to the size of a single order area, batch board can be subdivided into small batch board and large batch board. The main characteristics of the two are as follows: the mass production board is for individual consumers with large order scale; the small production board is for enterprise customers with high degree of customization.
Small batch boards are for enterprise customers with high degree of customization; there are many kinds of products, but the area of a single order is small, generally less than 50 square meters. Small batch boards are mainly used in communication equipment, industrial control and medical, aerospace, national defense and other fields. There are many types of products. The demand for single type of products is relatively small, but the degree of customization is high.
Mass production boards are for individual consumers with large orders. The downstream customers of large quantities of board terminals are generally for individual consumers, mainly used in consumer electronics fields such as computers and mobile terminals; there are not many kinds of products, but the single order area is large, and the order area is generally more than 50 square meters.
PCB Classification According to Different Needs of Customers
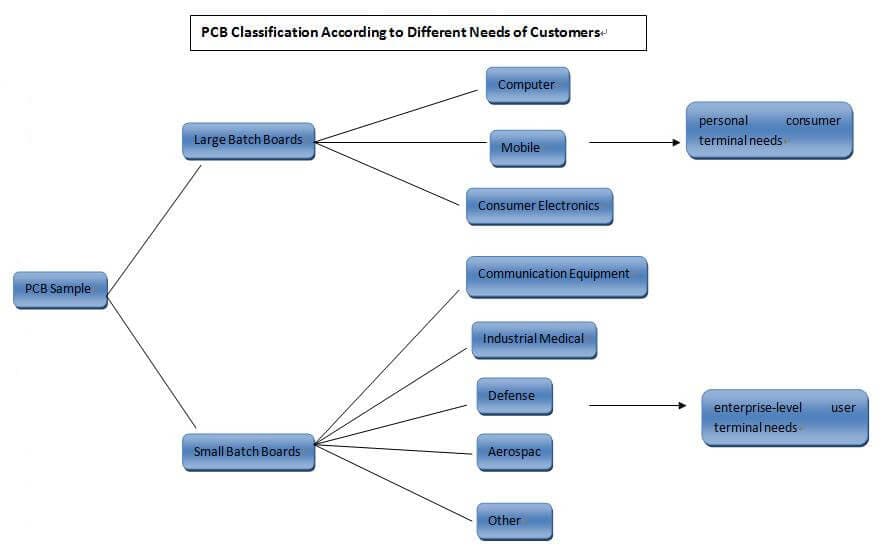
Because of the need to meet customer requirements for application scenarios, materials, area and performance parameters of the final product, both large and small batch boards are customized. In order to ensure the stability of the upstream, customers will not easily replace PCB suppliers, but will allocate order shares among different suppliers according to the quotation.
For mass enterprises, in order to obtain more order share and consolidate the relationship with downstream customers in order to obtain more market share, mass enterprises generally only guarantee a reasonable gross profit rate, and the quotation will not be too high. When the number of orders increases, large-scale board enterprises can reduce costs and improve efficiency by continuously expanding production capacity, and enter a virtuous circle with downstream customers.
However, the application fields of small batch PCB are mostly emerging medium and high-end fields, with higher degree of customization and short delivery time to customers. Due to the complexity and high technical difficulty of production process and process management brought by its many characteristics, customers have higher requirements on manufacturer’s technology and yield. Nowadays, there are few domestic medium and high-end small batch PCB manufacturers, so small batch PCB manufacturers have strong bargaining power on the downstream, and the gross profit rate of small batch PCB manufacturers is relatively higher under the same technical production conditions.
The Main Difference Between Large and Small Batch Boards
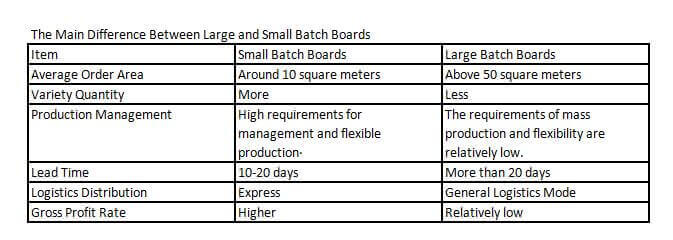
Although the gross profit rate of PCB small batch board is higher and the profit level of PCB small batch board is higher from the enterprise level, the core reason for the small number of PCB sample and small batch board manufacturers in China is that the technology of PCB R & D is relatively backward.
Technical barriers lead many PCB enterprises to flinch from the model market, R & D means investing a lot of time and money costs, and there are also higher requirements for enterprise personnel training and convening. In addition to technical factors, there are other factors that have become the pain points of the development of small batch PCB manufacturers.
Main Pain Points of Small Batch Board Manufacturers’ Development
- Technical barriers: the R & D, design and production of small batch boards require enterprises to have high-tech and talents.
- Fierce competition: domestic manufacturers started late, foreign manufacturers have formed a complete industrial chain development, and have a stable source of customers.
- Price rise of raw materials: it is greatly affected by copper, gold, oil and other bulk commodities in the international market.
- China’s environmental protection policy is becoming increasingly strict