Copper laying in PCB design is an important part of circuit board design. The so-called copper filling uses the idle space on the PCB as a reference plane and then fills it with solid copper. These copper areas are also called copper fillings. The significance of laying copper is to reduce the impedance of the ground wire, improve the anti-interference ability; reduce the voltage drop, improve the power supply’s efficiency, connect to the ground wire, and reduce the loop area. The copper cladding process plays a very critical role in the PCB process. Incomplete, truncated mirror loops or incorrectly positioned copper layers often cause new interference and negatively affect the use of the circuit board.
The Purpose of Copper Laying
- Enhance the heat dissipation function of the board,
- Mainly to enhance the anti-interference ability of the circuit board,
- Copper laying is mostly connected to the ground network.
- Three forms of copper pouring: full filling, grid form filling, and only boundary filling.
- Copper cladding is generally placed on the Bottom Layer and Top Layer, and Lock Primitives is to lock the copper cladding
- When wiring, the bottom line is generally not arranged, but the copper is reserved on the ground network, which connects all the grounds together.
- Select “Don’t Pour Over Same Net Object”, which means that the filling does not exceed the same net object, which is used to set the internal filling of the copper pour, and is not connected to the network; Select (the default is to select this) “Pour Over All Same Net Object”. That is, the filling is only performed in the same network, which is used to set the internal filling of copper pouring, as for the network boundary and pad connection; “Pour Over Same Net Polygons Only” is to fill all network objects, whether they are pads or vias.
- Remove Dead Copper to remove dead copper, which is an isolated copper skin.
- After entering the copper pour, select each location point and then draw a point to select the area. The space bar can adjust the line drawn in the area to adjust the angle or radian and direction.
- Assignment and pasting of copper pour: first draw the top layer of copper pour (you can also draw the bottom layer of copper pour first), then copy the top layer of copper pour, then select a key point, and then paste the copper pour, so that the copied The copper pour is also placed on the top layer, then select this copper pour (choose one of the two, either is acceptable), and then change the layer and network of the selected copper pour (basically the ground) (right-click the mouse, on the drop-down box that appears Select properties, and then modify the level and network on the dialog box that pops up).
Advantages and Disadvantages of PCB Copper Laying
Advantages
- For EMC (electromagnetic compatibility) requirements, large-area ground or power supply needs to be covered with copper, which will play a shielding role, and some special grounds, such as PGND (protective ground), will play a protective role.
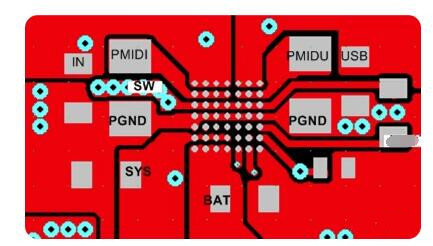
- For PCB manufacturing requirements, copper is laid on PCB layers with less wiring to ensure the uniform effect of electroplating copper plating or lamination without deformation and bending.
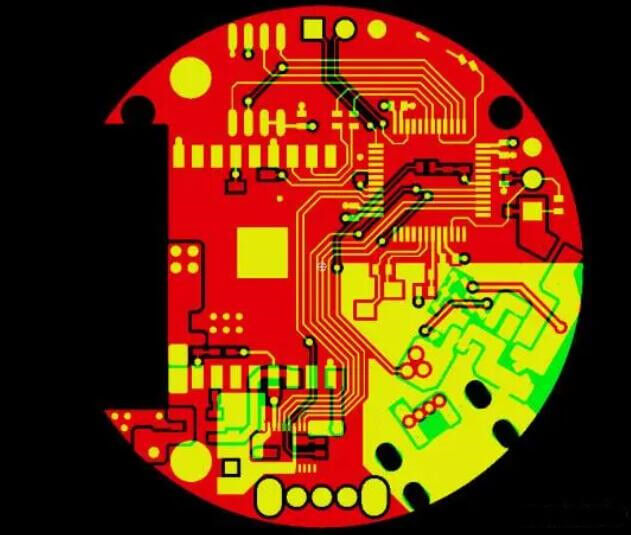
- For signal integrity requirements, give high-frequency digital signals a complete return path and reduce the wiring of the DC network. Of course, there are also reasons for heat dissipation. Special device installation requires copper laying, and so on.
Disadvantages
- If the component pins are fully covered with copper, it may cause excessive heat dissipation, making it difficult to desolder and repair. So sometimes to avoid this situation, a cross connection is used for components (pin contact and pad contact are “ten”).
- Placing copper in the area around the antenna will easily lead to weak signals, and the acquisition signal will be interfered with. The impedance of copper paving will affect the performance of the amplifier circuit. Therefore, the area around the antenna part is generally not covered with copper.
The Shape of PCB Copper
Solid shape copper
The solid copper clad has the dual functions of increasing the current and shielding. However, if the solid copper clad is subjected to wave soldering, there is a certain thermal expansion and contraction tension, and the board may warp or even bubble. Therefore, several slots are generally opened for solid copper cladding to relieve the tension and cause the copper foil to blister.
Grid shape copper
The grid is coated with copper, which mainly plays a shielding role, and the effect of increasing the current will be reduced. From the perspective of heat dissipation, grid copper not only reduces the heating surface of copper but also plays a certain role in electromagnetic shielding. However, the production process has certain requirements on the shape of the grid, and the grid is too small to affect the quality and yield.
Design of PCB Copper Laying
When designing a PCB, generally each surface of the PCB must be covered with copper and grounded. The main reason is to prevent PCB bending deformation, signal interference, and crosstalk.
Therefore, copper should be grounded when wiring. However, since many components and traces are on the outer layer, the copper foil will be divided into small isolated copper and slender copper skins by these component pads and their traces.
1. Handling broken copper
Those thin, long, and poorly grounded copper will have an antenna effect, which will cause poor EMC problems. Therefore, it is necessary to avoid causing broken copper when pouring as much as possible. If it causes broken copper, it can be deleted.
2. Dealing with isolated copper
Island (dead zone) copper problem, if the isolated copper is relatively small and equal to broken copper, it can be deleted. If it is very large, it can be defined as a certain ground to add vias, and there will be no isolated copper at this time.
PADS Light Painting File Copper Clad
The file designed by PADS needs to be paved again when it is opened for the second time. The reason is that the copper paving of PADS software is a linear copper skin, which is also characteristic of PADS software. The amount of data on the linear copper sheet is large. If you close the software and reopen the saved copper layer, the file will be very slow and stuck. Therefore, after the PADS software is closed, only the copper skin frame of the design file is retained.
PADS Copper Laying Method
1. Filling (hatch)
Filling is to restore the copper filling because the PADS software does not retain the entire designed copper skin, only the outer frame of the copper skin. So the second opening of the design file needs to restore the copper filling.
2. Flood
The copper filling is used for the first time after the PCB Layout is completed, or the PCB has changes (such as design rules) and copper filling needs to be used again.
3. Flat link
The plane connection refers to the copper skin of the inner layer. The reason is that the copper skin designed by the PADS software only retains the outer frame of the copper skin. When the copper skin of the inner layer of the design file is opened for the second time, the plane connection needs to be selected to restore the copper laying.
Therefore, when the PADS design file is output to the Gerber file, the second time the design file is opened, it must be refilled to restore the copper filling. If the board factory helps the design engineer output Gerber, it needs to restore the copper filling operation, otherwise, the output Gerber file lacks copper skin, resulting in manufacturing errors and the product cannot be used.
DFM Check Design Copper Laying
Regarding the manufacturability of broken copper and isolated copper, broken copper will be etched away due to the slender features during the manufacturing process, resulting in copper separation, falling off in other positions, and causing short circuits in different networks.
When the CAM engineer of the board factory processes the production documents for isolated copper, he will inquire and confirm with the design engineer because the isolated copper without a network connection is an abnormal design. Therefore, isolated copper in the design will waste communication costs and delay the production cycle.