Scratching is the most common and difficult problem in PCB factories. We can only control this defect at the lowest proportion by reminding ourselves to pay attention to the operation specifications at all times.
How to avoid scratching during PCB manufacturing?
Process 1: Cutting – fillet grinding
Reasons for Scratching: improper operation
How to avoid(Standard Process)?
- Check whether there are sundries and tools on the machine, and do not place them on the board.
- Handle with care. Do not drag the board to rub on the machine table. The placement board should be flat.
- Conduct irregular self-inspection, and place each 25pnl stack crosswise. Do not hit the plate surface with the plate corner when the angle is not worn.
- Handle with care. Do not drag between the plates, bruise the copper surface, and scratch. 50pnl is separated by a backing plate
Process 2: Drilling
Reasons for Scratching: improper operation
How to avoid(Standard Process)?
- Pay attention to the upper plate of the pin to avoid foreign matters, and place the plates with the pin staggered.
- When loading the multilayer board, you can only hold 1pnl at a time, and handle it gently.
- Handle the pin gently, and do not lose the board or drag the board.
4 during the grinding operation, the plate surface shall not be damaged between plates. - When turning the plate, every 50pnl is separated by a gasket, and each plate is not more than 200pnl.
- The second drill board must be inserted or separated before the second drill. After the second drill, it must also be separated or inserted into the next process.
Process 3: Electroplating – grinding plate
Reasons for Scratching: 1. Improper operation by operators 2. Machine jam.
How to avoid(Standard Process)?
- When placing plates, the distance between plates must be 3-5cm to prevent the stacking machine from jamming.
- Check the operation of the machine before starting it to prevent blocking.
- The circuit board must be inserted into the rack or separated from the film after grinding.
- Handle gently, and do not drop the board at the place where it is connected.
- Count and place the board with care, and do not lose the board or drag the board.
- Every 50pnl in the area to be transferred should be separated by a backing plate and film, and different types of plates should be separated by a backing plate and film.
Process 4: Electroplating – plate electricity
Reasons for Scratching: improper operation
How to avoid(Standard Process)?
- Handle with care when inserting the rack, and be careful not to hit the board surface.
- The boards to be inserted shall be placed neatly, and the boards shall not be loose or scattered.
- The plates after sinking PTH should be placed neatly and dried in time.
Process 5: Electroplating – Graphic electricity
Reasons for Scratching: improper operation
How to avoid(Standard Process)?
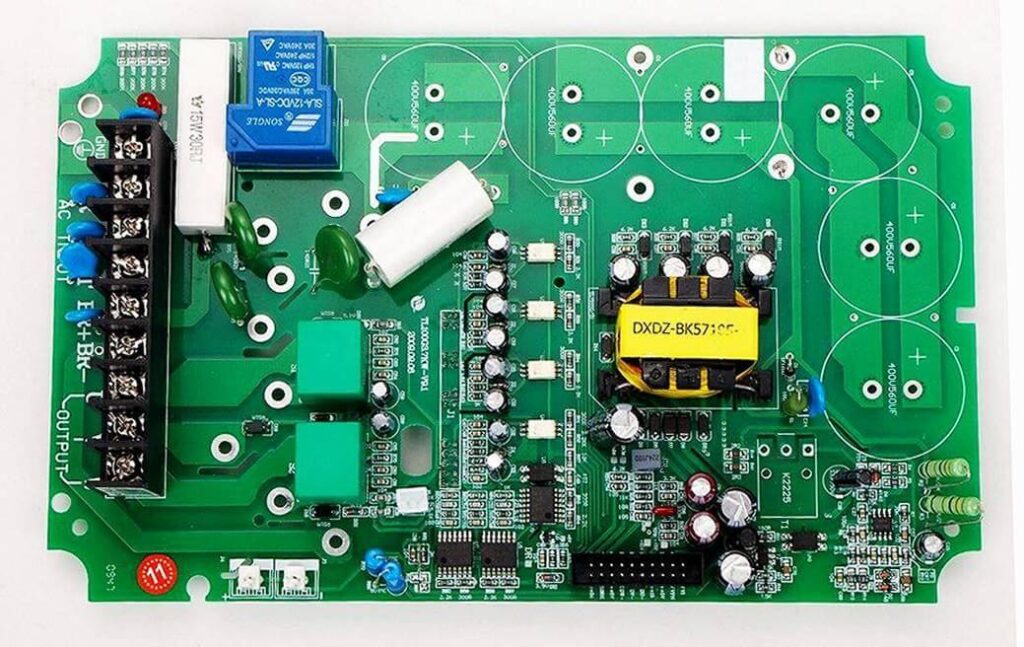
- Hold the splint with both hands, and only one at a time.
- Take the edge of the board and avoid the collision between the board and the board and other objects when putting it on the shelf.
- Pay attention to the accuracy of the board entering the slot, and put it down slowly to avoid scratching.
- When clamping the plate, check whether the screw pinches the line.
- Pay attention to the quality change of each cylinder plate. The upper and lower lines must hold only one plate in one hand.
- When turning to etch, only one plate can be inserted in each grid, and plates cannot be stacked between plates.
Process 6: Electroplating – etching
Reasons for Scratching: improper operation
How to avoid(Standard Process)?
- Place the board, work with gloves when connecting the board, handle it gently, and place the board at a distance of 2-3cm.
- Check the operation of the machine at any time.
- The etched board must be inserted into the frame and separated by the film to prevent flower arrangement.
- If there are unclean etched plates at the connecting plate, they should be treated in time. They should not be stacked together, and they must be separated from paper or inserted into a rack.
- The plates sent to each Aoi must be separated by film every PNL, no more than 200pnl per plate, and the film must be larger than the plate surface.
Process 7: Circuit – grinding board
Causes: 1. Improper operation by operators 2. Machine jam
How to avoid(Standard Process)?
- When moving the plate, the large plate is 25pnl once and the small plate is 50pnl once.
- It is not allowed to drag and collide on the board. When the plates are stacked together, a 50pnl stack must be separated from different types of plates by a backing plate and film.
- When placing the plate, do not place the long-scale plate obliquely, and the distance between the plates is 3-5cm.
- Handle with both hands, do not drag the frame, handle with care, and do not stack two layers on the sequence car.
- Do not stack plates, hold two plates in one hand, or drop plates at the plate connection of the plate grinder.
Process 8: Circuit – film pressing
Reasons for Scratching: improper operation
How to avoid(Standard Process)?
- Cut the film piece by piece and insert the frame.
- Only one plate can be inserted into each grid, and no plates can be stacked between plates.
- The broken dry film can not exceed 25pnl.
Process 9: Circuit – contraposition exposure
Reasons for Scratching: improper operation
How to avoid(Standard Process)?
- Cut the film piece by piece and insert the frame.
- Only one plate can be inserted into each grid, and no plates can be stacked between plates.
- The broken dry film can not exceed 25pnl.
Process 10: Circuit – Development
Causes: 1. Improper operation by operators 2. Machine jam
How to avoid(Standard Process)?
- When removing the film from the exposed plate, the counter holds the plate with one hand and tears the film with the other.
- The removed plate should be placed at the exposed plate at an angle of 45 degrees, and collision is not allowed.
- Before starting the machine, check whether the machine operates normally, and the distance between boards is 3-5cm.
- Connect the connecting plates one by one, and insert them into the rack. Do not stack them together.
Read Standard PCB Production Process(Two) to Avoid Scratching
Read Standard PCB Production Process(Three) to Avoid Scratching