With the continuous expansion of the market demand for portable electronic products, electronic devices are becoming more and more light, thin, short, small and multifunctional. In particular, the application of flexible board for high-density interconnect structure (HDI) will greatly promote the rapid development of flexible printed circuit technology. At the same time, with the development and improvement of printed circuit technology, the development, research and application of rigid-flex PCB are widely used. It is expected that the supply of flexible and hard PCB in the world will increase greatly in the future. At the same time, the durability and flexibility of the rigid-flex pcb board also make it more suitable for medical and military applications, and gradually erode the strength of the rigid PCB. However, the manufacturing process of soft and hard composite board is complex, and some key technical difficulties are difficult to control.
Basic Manufacturing Process of Rigid-flex PCB Board
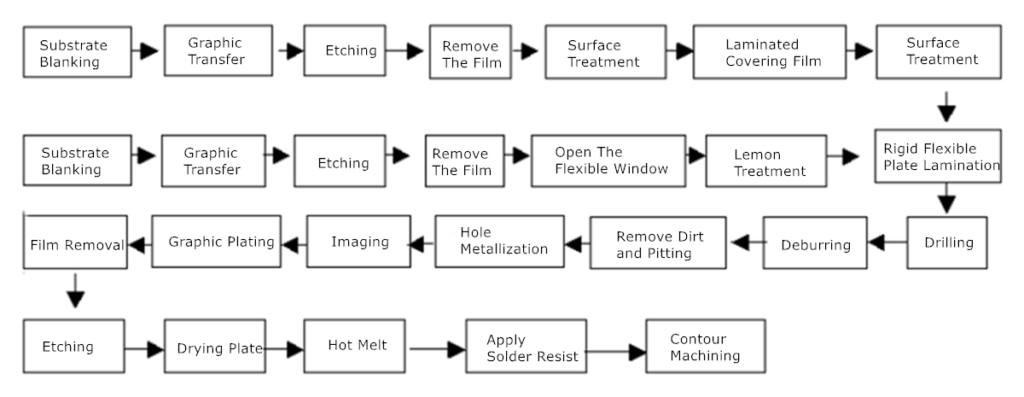
Product Design Features of Rigid-flex PCB Board
- Structural symmetry
- Single flexible plate
- The whole flexible plate is covered with a covering film
Ordinary four layer rigid-flex board for example, the processing flow is optimized, and the laminated structure is designed as shown in the figure below.
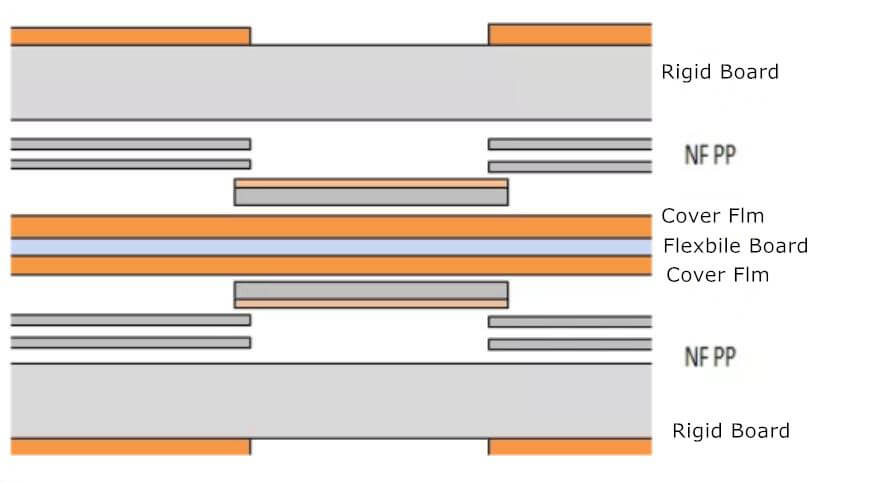
Difficulties in Production
Flexible Board
- Rigid PCB production equipment makes flexible boards. Because the soft board material is soft and thin, all horizontal lines of the soft board shall be carried by traction board to avoid scrapping the card board.
- After punching the positioning hole with ope, the single-chip processing before lamination also has a great impact on the interlayer alignment. Because polyimide materials are not resistant to strong alkali and swell in strong alkali solution, in the process of blackening and browning, the temperature and time shall be appropriately reduced in strong alkaline processes such as degreasing, blackening and browning.
- Because the flexible single sheet is easy to deform, the flatness before lamination is poor, and the resin fluidity of the adhesive sheet used is much lower than that of the semi cured sheet used for rigid plate lamination, in order to make the adhesive sheet combine well with the single sheet and embedded in the fine line spacing, we choose to use materials with good covering as the laminated liner materials, such as polypropylene film, polytetrafluoroethylene (PTFE) Silicone rubber sheet can improve the lamination quality of flexible plate
Rigid Board
- Whether it is substrate pressing or simple semi cured sheet pressing, pay attention to the consistency of the longitude and latitude direction of the glass cloth, and pay attention to eliminating thermal stress and reducing warpage during the pressing process.
- Soft and hard combination plate compression expansion and contraction control. Due to the poor expansion and contraction stability of the soft plate material, it is necessary to give priority to the production of the soft plate and the pressed PI covering film, and make the hard plate part according to its expansion and contraction coefficient.
- The flexible window is usually processed by milling first and then milling, but it needs to be processed flexibly according to the structure and thickness of the soft and hard combined plate,? If the flexible window is milled first, the milling accuracy shall be ensured, which can not affect the welding or the deflection