The development of electronic industry promotes the development of PCB, and also puts forward higher requirements for PCB manufacturing process and surface mount technology. The plug hole technology came into being. The plug hole of PCB circuit board is generally placed on the second layer with ink after the anti welding layer, so as to fill the heat dissipation hole with a hole diameter of less than 0.55mm.
Why do PCB boards need plug holes?
Via hole is also called through hole. In order to meet the requirements of customers, the through hole of circuit board must be plugged. After a lot of practice, the traditional aluminum plug hole process is changed, and the resistance welding and plug hole of circuit board surface are completed with white mesh, which has stable production and reliable quality.
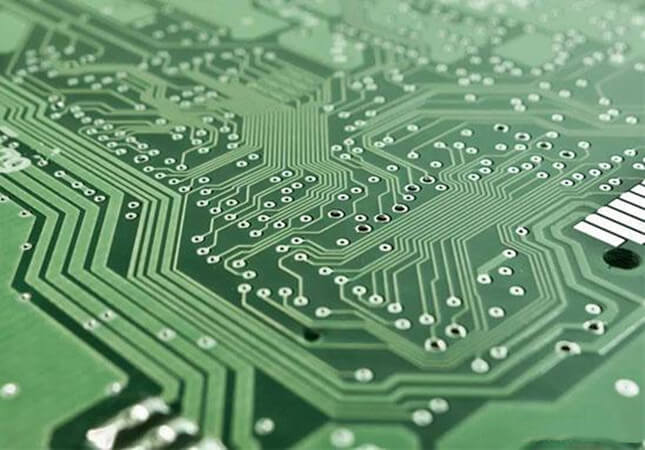
Via hole plays the role of connecting and conducting lines. The development of electronic industry also promotes the development of PCB, and puts forward higher requirements for PCB manufacturing process and SMT processing technology. The via hole plug process came into being and should meet the following requirements
- If there is copper in the through hole, it can be plugged but not plugged for resistance welding;
- There must be tin and lead in the through hole, with certain thickness requirements (4 microns). No solder resist ink shall enter the hole, resulting in tin beads in the hole;
- The through hole must be provided with solder resist ink plug hole, which is opaque, and there shall be no tin ring, tin bead, flatness and other requirements.
With the development of electronic products in the direction of “light, thin, short and small“, PCB is also developing to high density and high difficulty. Therefore, there are a large number of SMT and BGA PCBs, and customers require plug holes when installing components.
The Main Functions of Plug Holes
- Prevent short circuit caused by tin penetrating through the element surface from the through hole during PCB wave soldering; In particular, when we put the via on the BGA pad, we must first make the plug hole and then gold plating to facilitate the welding of BGA.
- Avoid residual flux in the through hole;
- After the SMT processing and component assembly of the electronic factory are completed, the PCB should absorb vacuum on the testing machine to form negative pressure.
- Prevent the surface solder paste from flowing into the hole, resulting in false welding and affecting the installation;
- Prevent tin beads from popping out during over wave soldering, resulting in short circuit.
The above is why we need to make plug holes for PCB making and the function of making plug holes for PCB making. Please contact us on how to need PCB prototyping.