Welding is an important part of the PCB design process. Welding is to fix electronic components on the PCB. In PCBA processing, wave soldering and reflow soldering are two common welding processes, but the welding methods used in different scenarios are different. What are the differences between the two welding processes?
Wave Soldering
Wave soldering is a batch PCB welding process, which is to weld the molten liquid tin at a high temperature with the component plug-in of the PCB board. The wave soldering process consists of four steps: flux spraying & precoating, preaheating, wave soldering, and cooling.
Flux: It’s mainly used to remove oxides on the plate, which can provide lower surface tension, thermal transmittance, and a smoother welding process.
Preheating: PCB is preheated and flux is activated through the hot channel.
Wave soldering: With increasing temperature, the solder paste becomes liquid, forming waves, and its edge plate will travel above it, so the components can be firmly bonded to the plate.
Cooling: Wave soldering curve conforms to temperature curve. As the temperature reaches the peak value during wave soldering, the temperature drops, which is called the cooling zone.
Wave Soldering Method
Wave soldering refers to the soldering of melted soft solder (lead-tin alloy) into a solder wave required by the design through an electric pump or an electromagnetic pump. It can also be formed by injecting nitrogen into the solder pool so that the printed board with components in advance can realize the soft soldering of mechanical and electrical connection between the component terminals or pins and the printed board pad through the solder wave. According to the waves of different geometric shapes used by the machine, wave soldering systems can be divided into many kinds.
Wave soldering process: insert the component into the corresponding component hole → precoat flux → pre-bake (temperature: 90-1000C, length: 1-1.2m) → wave soldering (220-2400C) → cut off excess plug-in pins → check.
Reflow Soldering
Reflow soldering refers to the permanent bonding of components on the bonding pad on the circuit board by the solder paste. The solder paste will be melted by hot air or other heat radiation conduction. There are four welding processes for reflow welding: preheating, heat preservation, reflow welding, and cooling.
Preheating: Preheating conforms to the thermal curve and can well remove volatile solvents that may include solder paste.
Thermal insulation: the board enters the thermal insulation area after being heated. Ensure that any area that is not completely heated due to the shadow effect reaches the necessary temperature. The other is to activate the flux and remove the solder paste solvent or volatiles.
Reflow welding: Reflow area is the area where the highest temperature is reached during welding. The solder melts here and forms the necessary solder joints. The actual reflow process refers to that the flux reducing the surface tension at the metal joint to achieve metallurgical bonding so that a single solder ball can be bonded and melted.
Cooling: It is required to conduct cooling without any pressure on the components of the cooling plate after reflux. Proper cooling can inhibit the formation of excessive intermetallic compounds or thermal shock to components.
Reflow Soldering Method
Different reflow soldering has different advantages, and the process flow is certainly different.
Infrared reflow soldering: high radiation heat conduction efficiency, large temperature gradient, easy to control the temperature curve, and easy to control the upper and lower temperature of PCB during double-sided soldering. Shadow effect, uneven temperature, easy to cause partial burning of components or PCB.
Hot air reflow welding: the convection conduction temperature is uniform and the welding quality is good. The temperature gradient is difficult to control.
Forced hot air reflow welding: infrared hot air mixed heating combines the advantages of infrared and hot air furnaces, which can obtain excellent welding effects during product welding. Forced hot air reflow welding can be divided into two types according to its production capacity:
- Temperature zone type equipment: mass production is suitable for mass production of PCB boards placed on the strip, which should pass through a number of fixed temperature zones in sequence. Too few temperature zones will cause a temperature jump, which is not suitable for welding high-density assembly boards. Moreover, it is large in size and high in power consumption.
- Small desktop equipment in temperature zone: small and medium-sized batch production is rapidly developed in a fixed space, and the temperature changes with time according to the set conditions, which is easy to operate. Repair of defective surface-mounted components (especially large components) is not suitable for mass production
Due to the characteristics of the reflow soldering process such as “reflow” and “self-positioning effect”, the requirements of the reflow soldering process on mounting accuracy are relatively loose, and it is easier to achieve high automation and high speed of welding. At the same time, because of the characteristics of reflow and self-positioning effect, the reflow soldering process has more strict requirements on pad design, component standardization, component end, PCB quality, solder quality, and process parameter settings.
Cleaning is a process of removing pollutants and impurities on the surface of the object to be cleaned by physical action and chemical reaction. In terms of solvent cleaning or water cleaning, surface wetting, dissolution, emulsification, saponification, etc. shall be carried out, and the dirt shall be stripped off the surface of the surface assembly plate by applying different mechanical forces, then rinsed or washed clean, and then blown, dried or naturally dried.
Reflow soldering is a key process in SMT production. A reasonable temperature curve setting is the key to ensuring the quality of reflow soldering. An inappropriate temperature curve will lead to incomplete welding, faulty soldering, component warping, excessive solder balls, and other welding defects on PCB, which will affect product quality.
SMT is a comprehensive system engineering technology, which covers substrate, design, equipment, components, assembly process, production accessories, and management. SMT equipment and SMT process require that the voltage at the operation site should be stable, electromagnetic interference should be prevented, static electricity should be prevented, good lighting and exhaust emission facilities should be provided, special requirements should be made for the temperature, humidity, air cleanliness, etc. of the operation environment, and operators should also receive professional technical training.
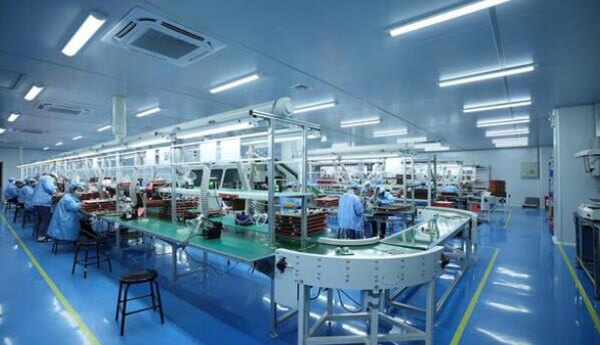
Difference Between Wave Soldering And Reflow Soldering
The first difference
The reflow soldering process is to realize the soft soldering of the mechanical and electrical connection between the solders of surface-mounted components or pins and the PCB pad by remelting the paste solder pre-allocated to the PCB pad.
Wave soldering has a new welding process for the enhancement of people’s awareness of environmental protection. In the past, the tin-lead alloy was used, but lead is a heavy metal that does great harm to the human body. So now there is lead technology. It uses * tin silver copper alloy * and special flux and requires higher welding temperature and higher preheating temperature. In addition, a cooling area workstation should be set up after the PCB passes the welding area. This is to prevent thermal shock. On the other hand, ICT will affect the detection.
Wave soldering can be basically interpreted as soldering for slightly larger and relatively small components, which is different from reflow soldering. Reflow soldering heats up the boards and components, in fact, it liquefies the solder paste painted on the boards to achieve the goal of connecting the components with the boards.
- Reflow soldering passes through preheating zone, reflow zone, and cooling zone. In addition, wave soldering is applicable to hand-inserting boards and glue dispensing boards, and all components are required to be heat-resistant. The wave-passing surface should not have components that used SMT solder paste. The SMT solder pasteboard can only be reflow soldered, and wave soldering is not allowed.
- Wave soldering is to melt the tin bar into a liquid state through the tin bath, and use the motor to stir to form waves so that PCB and parts can be welded together. It is generally used for the welding of hand plug-ins and SMT glue boards. Reflow soldering is mainly used in the SMT industry. It melts the solder paste printed on PCB and solders the components through hot air or other heat radiation conduction.
- Different processes: wave soldering needs to spray flux first, then through preheating, welding, and cooling zone.
The second difference between wave soldering and reflow soldering is: wave soldering is mainly used for welding plug-ins; Reflow soldering main patch-type components.
- Wave soldering is melting the tin bar into liquid through the tin bath, and using the motor to stir it to form waves so that PCB and parts can be welded together. It is generally used for the welding of hand plug-ins and the glue plate of SMT. Reflow soldering is mainly used in the SMT industry. It melts solder paste printed on PCB and solders components through hot air or other heat radiation conduction.
- Different processes: wave soldering requires spraying flux first, and then preheating welding, and cooling areas. Reflow soldering passes through preheating zone, reflow zone, and cooling zone. In addition, wave soldering is applicable to hand-inserting boards and glue dispensing boards, and all components are required to be heat-resistant. The wave-passing surface should not have components that used SMT solder paste. The boards of SMT solder paste can only be reflow soldered, and wave soldering is not allowed.
In short: wave soldering is mainly used for welding plug-in components, and reflow soldering is mainly used for soldering patch components. As far as welding is concerned, the difference between wave soldering and reflow soldering can never be ignored.