The basic purpose of PCB surface treatment is to ensure good solderability or electrical performance. Since copper in nature tends to exist in the form of oxide in the air, it is unlikely to remain original copper for a long time, so it needs other treatment.
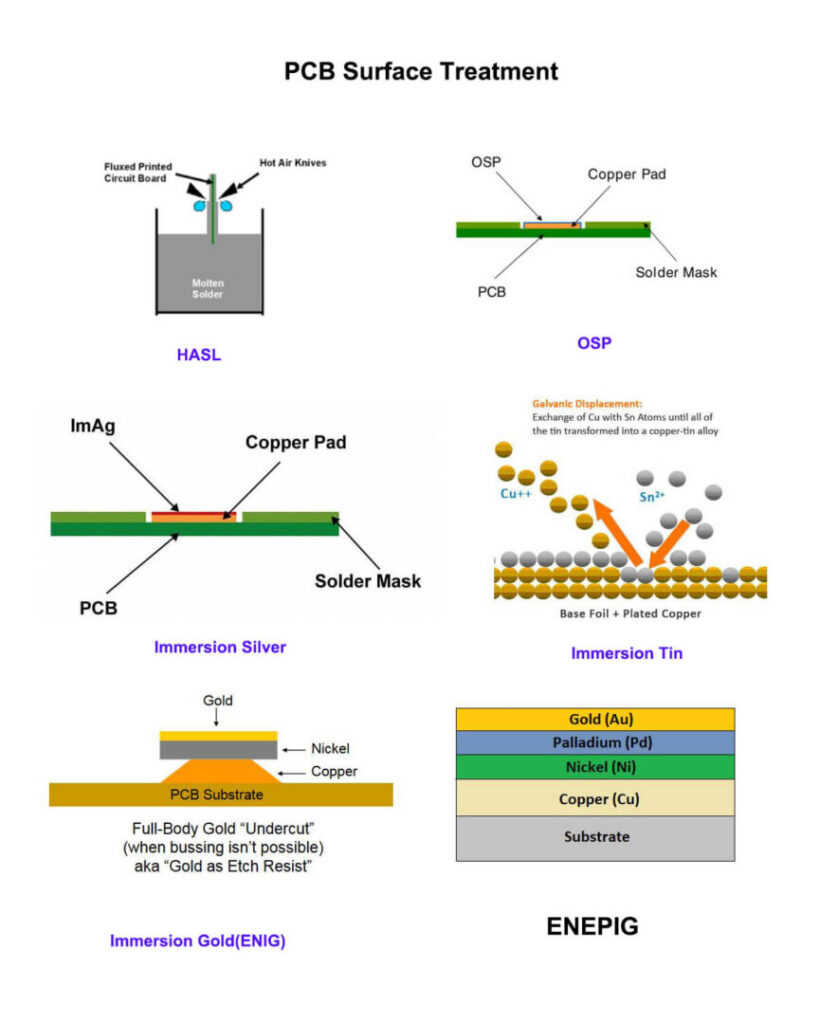
Comparison of 9 Current Mainstream PCB Surface Treatment Processes
Surface Treatment Process | Coating Characteristics | Manufacturing Cost | Thickness (μm) | Shelf Life |
Lead-Free HASL | The coating is uneven, which is mainly applicable to plates with large pad and wide line spacing Not applicable to HDI board: dirty process, bad smell, high temperature. | Medium and High | 2-5 on the pad, ≤ 5 in the hole
| 1 Year |
Hot Air Solder Level (HASL) | The difference between lead spraying and lead-free spraying is that the mechanical strength and brightness of lead spraying are better than that of lead-free spraying, but the lead in lead is harmful to human body, while lead-free spraying is not. | Medium and High | 2-5 on the pad, ≤ 5 in the hole
| 1 Year |
OSP (organic protective film)
| The coating is uniform and the surface is flat. Simple process, low price and good welding reliability. However, the appearance inspection is difficult. It is not suitable for repeated reflow to prevent scratches. | Minimum | 0.1-0.5 | Half a year |
Electroless Nickel Immersion Gold (ENIG) | The coating is uniform and the surface is flat. Good weldability, good contact and corrosion resistance, which can assist in heat dissipation. However, improper process control will lead to gold embrittlement, nickel corrosion (black disk) and poor welding of components. | High | Ni 3-5,Au 0.03-0.08 | 1 Year |
Electroless Nickel Electroless Palladium Immersion Gold(ENEPIG)
| The coating is uniform and the surface is flat. Good weldability, good contact and corrosion resistance. However, due to slow reaction rate and high requirements for production control, it is easy to have problems of black disk, gold surface pollution and gold surface discoloration. Nickel and palladium precipitation is actually an advanced version of gold precipitation, with only one more layer of palladium compared with gold precipitation. Palladium can prevent corrosion caused by replacement reaction and make full preparation for gold precipitation. This process is mostly used for high-end products and can cope with more precise and high-end electronic circuits. | High | Ni:2-5,Pd : 0.05-0.15, Au: 0.05-0.15 | Half a year |
Immersion Silver (Au) | The coating is uniform and the surface is flat. It has good weldability, can withstand many assembly operations, and the process is simple and fast. However, it has high requirements for environmental storage conditions and is prone to yellowing and discoloration. | Medium | 0.1-0.5 | Half a year |
Immersion Tin (Sn) | Uniform coating, flat surface and good weldability. But tin whiskers are difficult to control. Poor heat resistance, easy aging and discoloration. | Low | 0.8-1.2 | Half a year |
Electrolytic Nickel Gold
| Uneven coating, good contact, good wear resistance, weldable. However, gold is wasted, and it is difficult to guarantee the adhesion of solder resist printed on the gold surface. | Highest | Ni :3-5, Au:0.05
| 1 Year |
Electrolytic Hard Gold | The coating is uneven, with good contact, weldability, high smoothness, good discoloration resistance, and the most important thing is high hardness and excellent wear resistance. It is applicable to products with many times of plugging and unplugging. For example, gold fingers are usually plated with hard gold. Electrolytic hard gold belongs to electrolytic nickel gold. Electrolytic nickel gold is divided into hard gold and soft gold. Soft gold is mainly used for making gold wire during chip packaging; Hard metal is mainly used for electrical interconnection at non welded places. | Highest | 0.3-3 | 1 Year |
Influence of PCB surface treatment process on SMT patches
Physical Property | Hot air solder leveling (Known as HASL) | Immersion Tin | Immersion silver | OSP (organic protective film) | Electrolytic Nickel Gold (Hard Gold/Soft Gold) | Electroless Nickel Immersion Gold (ENIG) |
Storage Life (Months) | 12 | 12 | 12 | 6 | 6 | 6 |
Number of Backflows That Can be Experienced | 4 | 5 | 5 | 4 | 4 | 4 |
Cost | Medium | Medium | Medium | Low | High | High |
Process Complexity | High | Medium | Medium | Low | High | High |
Process Temperature (℃) | 250 | 50 | 70 | 40 | 55-60 | 80 |
Thickness Range (μm) | 1-25 | 0.05-0.2 | 0.8-1.2 | 0.2-0.5 | NI: 4-5; AU>0.05 | NI:3-5, AU:0.05-0.2 |