Scratching is the most common and difficult problem in PCB factories. We can only control this defect at the lowest proportion by reminding ourselves to pay attention to the operation specifications at all times.
How to avoid scratching during PCB manufacturing?
Before we list out the 20 processes to avoid scratching, following is the last processes.
Process 21: Text – packaging / outgoing
Reasons for Scratching: improper operation
How to avoid(Standard Process)?
- When pulling out the plate, the large plate on the turning cart shall not be stacked more than two layers, and only one piece is inserted in each grid of the iron frame.
- When moving and placing the board, it must be handled with care, and pay attention to the impact of the iron frame on the board surface.
- Pack each board with a paper sheet separated, and the paper sheet is larger than the board surface.
Process 22: Text – rework board
Reasons for Scratching: improper placement
How to avoid(Standard Process)?
- All reworked printed boards (including finished boards) must be placed in different areas and separated by paper sheets or shelves.
Process 23: Molding
Reasons for Scratching: improper operation
How to avoid(Standard Process)?
- The gold plates before and after the beer plate and the Gong plate, the paper larger than A4 and the variegated oil plates must be separated by paper or film.
- The formed board shall not be placed in the plastic basket horizontally or vertically. If this phenomenon occurs, it must be separated with hard paper, and it must be handled with care.
- There shall be no plate throwing and throwing.
- The placement height of the plate after punching is subject to 100pcs.
- The plates behind V-CUT must be placed neatly in different areas.
- The board transferred to the next sequence must be placed in the basket, and the board in the basket must not be shaken (filled with paper).
Process 24: Electric measurement – plate washing
Reasons for Scratching: 1. Improper operation. 2. Machine card
How to avoid(Standard Process)?
- The distance of placing the board and the speed of connecting the board must be matched to prevent the machine from getting stuck and the connecting board from getting busy.
- When connecting the board, the action should be standardized, and there should be no “shuffle” action.
- Do not take out all the paper and film when placing the board. Put one piece and take out one piece of paper.
Process 25: Electrical test – Test
Reasons for Scratching: 1. Improper operation
How to avoid(Standard Process)?
- Wear gloves during the test. Handle with care and place the board neatly.
- The OK Board shall be separated from the board to be repaired and placed neatly. 50set shall conduct self-inspection once, and there shall be no crushing and scratching.
- In the intermediate test of semi-finished products, each board shall be separated from the other by film or shelf.
- Handle the board gently in the process of measuring, and do not lose the board.
- The finished plate shall not be stacked higher than the stainless steel frame.
- Place the middle measuring plate no more than 200pnl.
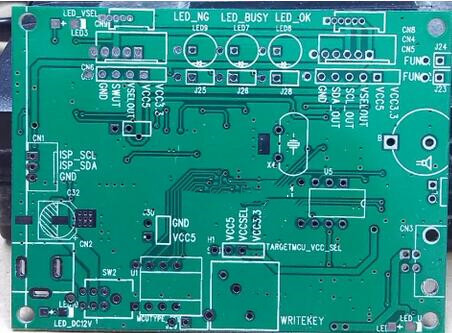
Process 26: Electrical measurement – finding and repairing
Reasons for Scratching: 1. Improper operation
How to avoid(Standard Process)?
- Take and place the plate vertically from the iron frame to prevent a collision.
- The repair tools should be positioned to prevent scratching the board.
- The stacking height of finished plates shall not exceed 100set.
Process 27: Electrical measurement – board out
Reasons for Scratching: 1. Improper operation
How to avoid(Standard Process)?
- Place them neatly and in order in the plastic frame, not horizontally or vertically.
- Intermediate measurement panel 25pnl, a stack of spacer films to turn the sequence, and handle the panel gently.
- The finished board 50 set is separated by a piece of Pearl sponge and paper.
Process 28: FQC
Reasons for Scratching: 1. Improper operation
How to avoid(Standard Process)?
- FQC plates to be inspected must be placed neatly. Wear gloves to handle the plates with care, and there must be no plate throwing.
- The problem Board shall be placed neatly for repair, and it shall not be placed horizontally to prevent scratching.
- When placing the board horizontally, there must be no hard objects below to prevent flower arrangement, green oil, and lines.
- Handle the Kanban with care. No “shuffle” action is allowed
Process 29: IQC/ Planning Department
Reasons for Scratching: 1. Improper operation 2. Improper placement
How to avoid(Standard Process)?
- When transporting large materials, pay attention not to hit the wall and foreign matters on both sides, and place the large materials smoothly.
- When picking and issuing materials, do not put hard objects and corresponding tools on large materials.
- When inspecting large materials, two people must lift their heads, and do not drag or impact.
- IQC works with gloves, handle with care, and does not scratch the copper surface.
- All boards sent out by the planning department must be stacked with 25pnl per package, and each PNL must be separated by film, and the paper must be larger than the board surface.
Process 30: Comprehensive
Reasons for Scratching: plate turning method
How to avoid(Standard Process)?
- The next process conducts random inspection on the incoming materials of the previous process, and those that cannot be directly shipped can be rejected if they are found to have scratches.
The plate can be closed only after the plate is repaired in the previous process. - For plates larger than A4 paper size, after CNC production, the paper must be separated and stacked every 50set before switching to the next process.
- All gold plates and plates with variegated oil (except small plates) must be separated from the paper before they can be transferred to the next process.
Read Standard PCB Production Process(One) to Avoid Scratching
Read Standard PCB Production Process(Two) to Avoid Scratching