Refer to PCB manufacturing process, after the PCB has been PTH(plated through hole) & PP(Panel Plating), it is time to do Membrane Pasting. A layer of blue dry film is pressed on the laminated circuit board. The dry film is a carrier and is very important in the circuit process. The dry film process is also named after it. Compared with wet film, dry film has higher stability and better quality, and can be directly used as non-metalized vias.
PCB Membrane Pasting
Dry Film
When attaching the film, first peel off the polyethylene protective film from the dry film, and then paste the dry film resist on the copper clad board under heating and pressurizing conditions. The resist layer in the dry film becomes soft after being heated, and its fluidity increases. The film is completed by the pressure of the hot pressing roller and the action of the adhesive in the resist.
The filming is usually done on a filming machine. There are many models of filming machines, but the basic structure is roughly the same: the film can be applied continuously or single-posted. Pay attention to the alignment of the dry film on the upper and lower dry film feed rollers during continuous film application. When single-posting, the size of the film should be slightly smaller than the board surface to prevent the resist from sticking to the heat press roller. The continuous film production efficiency is high, and it is suitable for mass production. The single-posting method can be used for small batch production to reduce the waste of dry film.
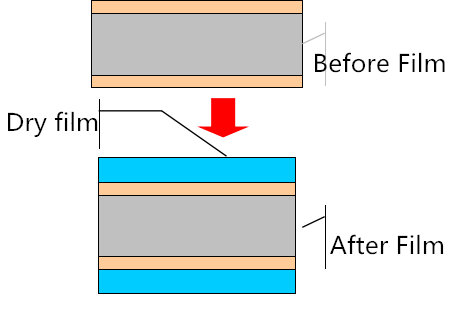
Tips: The three elements that must be mastered when applying the film are pressure, temperature, and transmission speed.
- Pressure
For the newly installed film laminator, first adjust the upper and lower hot pressing rollers to be axially parallel, and then use the method of gradually increasing the pressure to adjust the pressure, according to the thickness of the printed board, to make the dry film easy to stick, stick firmly and not Wrinkles. After the pressure is adjusted, it can be used in a fixed manner without frequent adjustment. The general line pressure is 0.5-0.6 kg/cm. - Temperature
It varies slightly according to the type, performance, ambient temperature and humidity of the dry film. If the film is dry, the ambient temperature is low, and the humidity is low, the film temperature should be higher, and vice versa. If the film temperature is too high, the image of the dry film will become brittle, and the plating resistance will be poor. If the film temperature is too low, the dry film will not adhere firmly to the copper surface, and the film will tend to warp or even fall off during the development or electroplating process. The temperature of the film is usually controlled at about 100°C. - Transmission Speed
The conveying speed is related to the film temperature. The higher the temperature, the faster the conveying speed, and the lower the temperature, the slower the conveying speed. Usually the transmission speed is 0.9 to 1.8 m/min.
In mass production, under the required conveying speed, it is difficult for the hot press roller to provide enough heat, so it is necessary to preheat the board to be filmed, that is, dry in the oven and cool it down for a while.
Wet Film
In order to adapt to the production of fine wire printed boards, a wet filming process has been developed. This process uses a special filming machine to form a water film on the surface of the copper foil before applying the dry film. The function of the water film is to improve the dry film. The fluidity of the film; removes the air bubbles remaining on the parts such as scratches, blisters, pits and fabric depressions; in the process of heating and pressing the film, the water increases the viscosity of the photoresist, which can greatly improve the dry film and the substrate Adhesion to improve the yield of fine wires. The qualified rate of fine wires can be increased by 1-9% by adopting this process.
The intact film should have a smooth surface, no wrinkles, no bubbles, no dust particles and other inclusions.
In order to maintain the stability of the process, 15 minutes of cooling and recovery period should be passed after the film is applied before exposure.