Printed circuit boards (PCBs) are widely used in various electronic devices. You can find them in mobile phones, computers and complex machines. If the PCB has defects or manufacturing problems, it may cause the final product to fail and cause inconvenience. In these cases, the manufacturer will have to recall these equipment and spend more time and resources to repair the fault. Therefore, PCB testing has become an indispensable part of the PCB manufacturing process. It finds problems in time, assists the staff to deal with them quickly, and ensures the high quality of PCB.
Let’s learn about 13 common PCB test methods.
1. On Line Test (ICT)
ICT( automatic online test) is a necessary test equipment for modern PCB manufacturers, which is very powerful. It is mainly used to detect the open circuit, short circuit and fault condition of all parts of PCBA through the test probe contacting the test points out of PCB layout, and clearly inform the staff. ICT has a wide range of applications, high measurement accuracy and clear indication of detected problems. Even workers with average electronic technology can easily handle PCBA with problems. Using ICT can greatly improve production efficiency and reduce production costs.
2. Flying Probe Test
Flying probe test and on-line test (ICT) are both recognized effective test forms. Both of them can effectively find production quality problems. However, flying probe test has proved to be a particularly cost-effective method to improve circuit board standards. In contrast to the traditional test method of fixing the test probe in place, the flying probe test uses two or more independent probes and runs without a fixed test point. These probes are electromechanical controlled and move according to specific software commands. Therefore, the initial cost of flying needle test is low. It can be completed by modifying the software without changing the fixed structure. In contrast, the initial fixture cost of ICT is higher, so for small batch orders, flying needle test is cheaper, but ICT is faster and less error prone than flying needle test, so ICT is more cost-effective for large batch orders.
3. Functional Test
Functional system test uses the special test equipment in the middle and end of the production line to comprehensively test the functional modules of the circuit board to confirm the quality of the circuit board. Functional tests mainly include final product test and hot mock up. Functional testing usually does not provide in-depth data (such as pin position and component level diagnosis) to improve the process, but requires special equipment and specially designed test procedures. Writing the function test program is very complex, so it is not suitable for most circuit board production lines.
4. Automatic Optical Inspection (AOI)
AOI uses a single 2D camera or two 3D cameras to take PCB photos, and then compares the PCB photos with the detailed schematic diagram. If the circuit board does not match the schematic diagram to a certain extent, the mismatch of the circuit board will be marked for inspection by technicians, and AOI can detect the fault problem in time. However, AOI testing will not supply power to the circuit board, and can not 100% detect the problems of all components. Therefore, AOI is generally used in combination with other testing methods. The common test combinations are
- AOI and flying probe test
- AOI and ICT test
- AOI and functional test
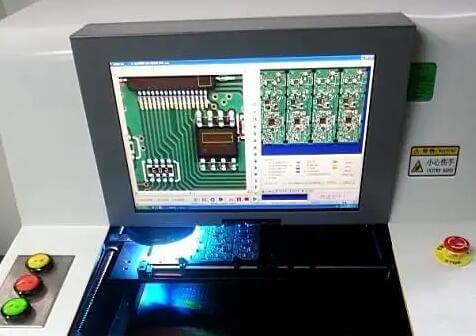
5. X-ray Test
X-ray testing uses low-energy X-rays to quickly detect open circuit, short circuit, empty soldering, missing soldering and other problems of circuit boards. X-ray is mainly used to detect ultra-fine spacing and ultra-high density defective circuit boards, as well as bridging, chip missing, dislocation and other defects during assembly. It can also use tomography to detect internal defects in IC chips. This is the only way to test the bonding quality of ball grid array and solder ball. The main advantage is that BGA Solder quality and embedded components can be checked without the cost of fixtures.
6. Laser Detection
This is the latest development of PCB testing technology. It scans the printed board with a laser beam, collects all measured data, and compares the actual measured value with the preset acceptance limit. This technology has been verified on bare board and is being considered for assembly board testing. This speed is enough for the mass production line. Its main advantages are fast output, no fixture and unobstructed vision. Its main disadvantages are high initial cost, maintenance and use problems.
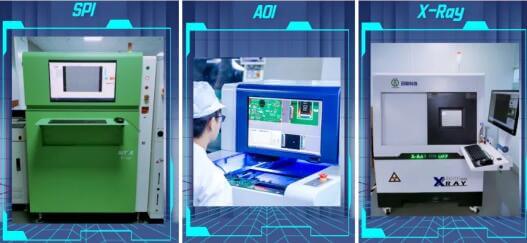
7. Aging Test
Aging test refers to the process of simulating various factors involved in the actual use conditions of products to conduct corresponding condition strengthening tests on the aging of products. The purpose is to test the stability and reliability of the product in a specific environment. According to the design requirements, place the product under specific temperature and humidity conditions, continuously simulate the work for 72 hours to 7 days, record the performance data, and reverse the production process for improvement to ensure that its performance meets the market demand. Aging test usually refers to electrical performance test. Similar tests include drop test, vibration test, salt spray test, etc.
In addition to the above 7 tests, other test methods will be used to further ensure PCB quality based on product requirements. For example:
8. Solderability Test
Ensure solid surface and increase the chance of forming reliable solder joints.
9. PCB Contamination Test
Detect a large number of ions that may contaminate the circuit board, cause corrosion and other problems.
10. Microsection Analysis
Investigation of defects, open circuits, short circuits and other faults.
11. Time domain reflectometer (TDR)
Fault of high frequency board found.
12. Peel Test
Find out the strength measurement required to peel the laminate from the plate.
13. Floating Soldering Test
Determining the thermal stress level that PCB holes can resist PCBA test is a necessary process. If it is completed correctly, it can prevent quality problems from damaging the brand reputation when the product is on the market.
OLINAPCB PCB manufacturing adopts first-class testing equipment, follows strict testing procedures, and is committed to providing customers with high reliability and high quality circuit boards.